安锻产品
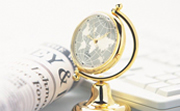
钢的淬火知识大全及淬火问题原因分析
淬火的定义与目的
将钢加热到临界点Ac3(亚共析钢)或Ac1(过共析钢)以上某一温度,保温一段时间,使之全部或部分奥氏体化,然后以大于临界淬火速度的速度冷却,使过冷奥氏体转变为马氏体或下贝氏体组织的热处理工艺称为淬火。
淬火的目的是使过冷奥氏体进行马氏体或贝氏体转变,得到马氏体或下贝氏体组织,然后配合以不同温度的回火,以大幅提高钢的强度、硬度、耐磨性、疲劳强度以及韧性等,从而满足各种机械零件和工具的不同使用要求。也可以通过淬火满足某些特种钢材的铁磁性、耐蚀性等特殊的物理、化学性能。
钢件在有物态变化的淬火介质中冷却时,其冷却过出一般分为以下三个阶段:蒸汽膜阶段、沸腾阶段、对流阶段。
钢的淬透性
淬硬性和淬透性是表征钢材接受淬火能力大小的两项性能指标,它们也是选材、用材的重要依据。
1.淬硬性与淬透性的概念
淬硬性是钢在理想条件下进行淬火硬化所能达到的最高硬度的能力。决定钢淬硬性高低的主要因索是钢的含碳量,更确切地说是淬火加热时固溶在奥氏体中的含碳量,含碳量越离,钢的淬硬性也就越高。而钢中合金元素对淬硬性的影响不大,但对钢的淬透性却有重大影响。
淬透性是指在規定条件下,决定钢材淬硬深度和硬度分布的特性。即钢淬火时得到淬硬层深度大小的能力,它是钢材固有的一种属性。淬透性实际上反映了钢在淬火时,奥氏体转变为马氏体的容易程度。它主要和钢的过冷奥氏体的稳定性有关,或者说与钢的临界淬火冷却速度有关。
还应指出:必须把钢的淬透性和钢件在具体淬火条件下的有效淬硬深度区分开来。钢的淬透性是钢材本身所固有的属性,它只取决于其本身的内部因素,而与外部因素无关;而钢的有效淬硬深度除取决于钢材的淬透性外,还与所采用的冷却介质、工件尺寸等外部因索有关,例如在同样奥氏体化的条件下,同一种钢的淬透性是相同的,但是水淬比油淬的有效淬硬深度大,小件比大件的有效淬硬深度大,这决不能说水淬比油淬的淬透性髙。也不能说小件比大件的淬透性高。可见评价钢的淬透性,必须排除工件形状、尺寸大小、冷却介质等外部因素的影响。
另外,由于淬透性和淬硬性也是两个概念,因此淬火后硬度髙的钢,不一定淬透性就髙;而硬度低的钢也可能具有很髙的淬透性。
2.影响淬透性的因素
钢的淬透性取决于奥氏体的稳定性。凡是能提高过冷奥氏体的稳定性,使C曲线右移, 从而降低临界冷却速度的因素,都能提髙钢的淬透性。奥氏体的稳定性主要取决于它的化学成分、晶粒大小和成分均匀性,这些与钢的化学成分和加热条件有关。
3.淬透性的测定方法
钢的淬透性的测定方法很多,常用的有临界直径测定法和端淬试验法。
(1)临界直径测定法 钢材在某种介质中淬冷后,心部得到全部马氏体或50%马氏体组织时的最大直径称为临界直径,以Dc表示。临界直径测定法就是制作一系列直径不同的圆棒,淬火后分别测定各试样截面上沿直径分布的硬度U曲线,从中找出中心恰为半马氏体组织的画棒,该圆棒直径即为临界直径。临界直径越大,表明钢的淬透性越高。
(2)端淬试验法 端淬试验法是用标准尺寸的端淬试样(Ф25mm×100mm),经奥氏体化后,在专用设备上对其一端面喷水冷却,冷却后沿轴线方向测出硬度-距水冷端距离的关系曲线的试验方法。 端淬试验法是猁定钢的淬透性的方法之一,其优点是操作简便,适用范围广。
4.淬火应力、变形及开裂
(1)淬火时工件的内应力 工件在淬火介质中迅速冷却时,由于工件具有一定尺寸,热传导系数也为一定值,因此在冷却过程中工件内沿截面将产生一定温度梯度,表面温度低,心部温度高,表面和心部存在着温度差。在工件冷却过程中还伴随着两种物理现象:一是热膨胀,随着温度下降,工件线长度将收缩;另一个是当温度下降到马氏体转变点时发生奥氏体向马氏体转变,这将使比体积增大。由于冷却过程中存在着温差,因而沿工件截面不同部位热膨胀量将不同,工件不同部位将产生内应力;由于工件内温差的存在,还可能出现温度下降快的部位低于点,发生马氏体转变,体积胀大,而温度髙的部位尚高于点,仍处于奥氏体状态,这不同部 位由于比体积变化的差别,也将产生内应力。因此,在淬火冷却过程中可能产生两种内应力:一种是热应力;另一种是组织应力。
根据内应力的存在时间特性还可分为瞬时应力和残余应力。工件在冷却过程中某一时刻所产生的内应力叫瞬时应力;工件冷却终了,残存于工件内部的应力称为残余应力。
热应力是指工件在加热(或冷却)时,由于不同部位的温度差异,而导致热胀(或冷缩)的不一致所引起的应力。
现以一实心圆柱体为例,说明其冷却过程中内应力的形成及变化规律。这里仅讨论其轴向应力。冷却刚开始时,由于表面冷却快,温度低,收缩多,而心部则冷却悝,温度髙,收缩小,表里相互牵制的结果,就在表层产生了拉应力,心部则承受着压应力。随着冷却的进行,表里温差增大,其内应力也相应增大,当应力增大到超过该温度下的屈服强度时,便产生了塑性变形。由于心部的渥度髙于表层,因而总是心部先行沿轴向收缩。塑性变形的结 果,使其内应力不再增大。冷却到一定时间后,表层温度的降低将逐渐减慢,则其收缩量也逐渐减小。而此时心部则仍在不断收缩,于是表层的拉应力及心部压应力将逐渐减小,直至消失。但是随着冷却的继续进行,表层湿度越来越低,收缩量也越来越少,甚至停止收缩。而心部由于温度尚高,还要不断地收缩,最后在工件表层形成压应力,而心部则为拉应力, 但由于温度已低,不易产生塑性变形,所以这应力将随冷却的进行而不断增大,并最后保留于工件内部,成为残余应力。
由此可见,冷却过程中的热应力开始是使表层受拉,心部受压,而最后留下的残余应力则是表层受压,心部受拉。
综上所述,淬火冷却时产生的热应力是由于冷却过程中截面温度差所造成的,冷却速度越大,截面温差越大,则产生的热应力越大。在相同冷却介质条件下.工件加热温度越高、 尺寸越大、钢材热传导系数越小,工件内温差越大,热应力越大。工件若在高温时冷却不均 匀,将会发生扭曲变形。工件若在冷却过程中产生的瞬时拉应力大于材料的抗拉强度时,将会产生淬火裂纹。
相变应力是指热处理过程中由于工件各部位相转变的不同时性所引起的应力,又称组织应力。
淬火快冷时,当表层冷至Ms点,即产生马氏体转变,并引起体积膨胀。但由于受到还 没进行转变的心部的阻碍,使表层产生压应力,而心部则为拉应力,应力足够大时,即会引起变形。当心部冷至Ms点时,也要进行马氏体转变,并体积膨胀,但由于受到已经转变的 塑性低、强度高的表层的牵制,因此其最后的残余应力将呈表面受拉,心部受压。由此可见,相变应力的变化情况及最后状态,恰巧与热应力相反。而且由于相变应力产生于塑性较低的低温下,此时变形困难,所以相变应力更易于导致工件的开裂。
影响相变应力大小的因素很多,钢在马氏体转变温度范围的冷却速度越快、钢件的尺寸越大、钢的导热性越差、马氏体的比体积越大,其相变应力就越大。另外,相变应力还与钢的成分、钢的淬透性有关,例如,高碳髙合金钢由于含碳量高而增大马氏体的比体积,这本应增加钢的相变应力,但随着含碳量升高而使Ms点下降,又使淬火后存在着大量残余奥氏体,其体积膨胀量减小,残余应力就低。
(2)淬火时工件的变形 淬火时,工件发生的变形主要有两类:一类是工件几何形状的变化,它表现为尺寸及外形的变化,常称为翘曲变形,是淬火应力所引起的;另一类是体积变形,它表现为工件体积按比例胀大或缩小,是相变时的比体积变化所引起的。
翘曲变形又包括形状变形和扭曲变形。扭曲变形主要是加热时工件在炉内放置不当,或者淬火前经变形校正后没有定型处理,或者是由于工件冷却时工件各部位冷却不均匀所造成的。这种变形可以针对具体情况分析解决。下面主要讨论体积变形和形状变形。
1)淬火变形的原因及其变化规律
组织转变引起的体积变形 工件在淬火前的组织状态一般为珠光体型,即铁素体和渗碳体的混合组织,而淬火后为马氏体型组织。这些组织的比体积不同,将引起淬火前后体积变化,从而产生变形。但这种变形只按比例使工件胀缩,因而不改变工件形状。
另外,热处理后组织中的马氏体量越多,或者马氏体中含碳量越高,则其体积膨胀就越多,而如残余奥氏体量越多,则体积膨胀就越少。因此热处理时可以通过控制马氏体和残余輿氏体的相对含量来控制其体积变化,如控制得当,可使其体积旣不膨胀,也不缩小。
热应力引起的形状变形 热应力引起的变形发生在钢件屈脤强度较低、塑性较高、而表面冷却快、工件内外温差最大的髙温区。此时瞬时热应力为表面张应力和心部压应力, 由于这时心部温度高,屈服强度比表面低得多,因此表现为在多向压应力作用下的变形,即立方体向呈球形方向变化。其结果是尺寸较大的一方缩小,而尺寸较小的一方则胀大。例如长圆柱体长度方向缩短,直径方向胀大。
组织应力引起的形状变形 组织应力引起的变形也产生在早期组织应力最大的时刻。此时截面温差较大,心部温度较髙,仍处于奥氏体状态,塑性较好,屈服强度较低。瞬时组织应力是表面压应力和心部拉应力。因此变形表现为心部在多向拉应力作用下的拉长,其结果是在组织应力作用下,工件中尺寸较大的一方伸长,而尺寸较小的一方缩短。例如长圆柱体组织应力引起的变形是长度伸长,直径缩小。
表5.3为各种典型钢件的淬火变形规律。
淬火的目的是使过冷奥氏体进行马氏体或贝氏体转变,得到马氏体或下贝氏体组织,然后配合以不同温度的回火,以大幅提高钢的强度、硬度、耐磨性、疲劳强度以及韧性等,从而满足各种机械零件和工具的不同使用要求。也可以通过淬火满足某些特种钢材的铁磁性、耐蚀性等特殊的物理、化学性能。
钢件在有物态变化的淬火介质中冷却时,其冷却过出一般分为以下三个阶段:蒸汽膜阶段、沸腾阶段、对流阶段。
淬硬性和淬透性是表征钢材接受淬火能力大小的两项性能指标,它们也是选材、用材的重要依据。
2)影响淬火变形的因素
影响悴火变形的因素主要为钢的化学成分、原始组织、零件的几何形状及热处理工艺等。
(3)淬火裂纹 零件产生裂纹主要发生在淬火冷却的后期,即马氏体相变基本结束或完全冷却后,因零件中存在的拉应力超过钢的断裂强度而引起脆性破坏。裂纹通常垂直于最大拉伸变形方向,因此零件产生不同形式的裂纹主要取决于所受的应力分布状态。
常见的淬火裂纹的类型:纵向(轴向)裂纹主要在切向的拉伸应力超过该材料的断裂强度时产生;当在零件内表面形成的大的轴向拉应力超过材料断裂强度时形成横向裂纹 ;网状裂纹是在表面二向拉伸应力作用下形成的;剥离裂纹产生在很薄的淬硬层内,当应力发生急剧改变并在径向作用着过大拉应力时将可能产生这种裂纹。
纵向裂纹又称轴向裂纹。裂纹产生于零件表层附近最大拉应力处,并裂向心部有一定深度,裂纹走向一般平行轴向,但零件存在应力集中时或存在内部组织缺陷时也可改变走向。
工件完全淬透后,容易产生纵向裂纹,这与淬透工件表层存在较大切向拉应力有关,并随钢的含碳量提髙,形成纵向裂纹的倾向增大。低碳钢因马氏体比体积小,而且热应力作用强,表面存在着很大的残余压应力,故不易淬裂,随着含碳量提高,表层压应力减小,组织应力作用增强,同时拉应力峰值移向表面层,因此,高碳钢在过热情况下易形成纵向淬裂。
零件尺寸直接影响残余应力大小及分布,其淬裂倾向也不同。在危险截面尺寸范围内淬火也很容易形成纵向裂纹。此外,钢的原材料块陷也往往造成纵向裂纹。由于大多数钢件是由轧制成材的,钢中非金屑夹杂物、碳化物等沿着变形方向分布,致使钢材各向异性。如工具钢存在带状组织,淬火后其横向的断裂强度比纵向小30%〜50%外,如果钢中存在非金屑夹杂物等导致应力集中的因索,即使在切向应力比轴向应力小的情况下也容易形成纵向裂纹。为此,严格控制钢中非金属夹杂物、礙化糖级别是防止淬火裂纹的重要因素。
横向裂纹和弧形裂纹的内应力分布特征是:表面受压应力,离开表面一定的距离后,压应力变为很大的拉应力,裂纹产生在拉应力的蜂值区域内,然后当内应力重新分布或钢的脆性进一步增加时才蔓延到零件表面。
横向裂纹常发生在大型的轴类零件上,如轧辊,汽轮机转子或其他轴类零件。其裂纹特点是垂直于轴线方向,由内往外断裂,往往在未淬透情况下形成,属于热应力所引起。大锻件往往存在着气孔、夹杂物、锻造裂缝和白点等冶金缺陷,这些缺陷作为断裂的起点,在轴向拉应力作用下断裂。弧形裂缝诅是由热应力引起的,通常在零件形状突变的部位以弧形分布。主要产生于工件内部或尖锐棱角、凹槽及孔洞附近,呈弧形分布,当直径或厚度为80〜100mm以上的高碳钢制件淬火没有淬透时,表面呈压应力,心部呈拉应力,在淬硬层至非淬硬层的过渡区,出现最大拉应力,弧形裂纹就发生在这些区域。另外在尖锐棱角处的冷却速度快,全部淬透,在向平缓部位过渡时,也就是向未淬硬区过渡,此处出现最大拉应力区,因而容易产生弧形裂纹。工件的销孔、凹槽或中心孔附近的冷却速度较慢,相应的淬硬层较薄,在淬硬过渡区附近拉应力也易引起弧形裂纹。
网状裂纹又称表面龟裂,是一种表面裂纹。裂纹的深度较浅,一般在 0.01〜1.5mm左右。这种裂纹的主要特征是:裂纹具有的任意方向与零件的外形无关。许 多裂纹相互连接构成网状,且分布较广。当裂纹深度较大时,如达到1mm以上,网状特征消失,变成任意取向或纵向分布的裂纹。网状裂纹与表面受两向拉应力状态有关。
表面具有脱碳层的髙碳或渗碳钢零件,淬火时容易形成网状裂纹。这是由于表层比内层的马氏体含碳低,比体积小,淬火时使联碳的表层受到拉应力作用。在机械加工中未完全除去脱磷层的零件在高頻或火焰表面淬火时也会形成网状裂纹,为避免此类裂纹应严格控制零 件表面质量,热处理时应尽量防止氧化雎接现象。另外,锻模使用一定时间后,型腔中出现的成条排列或网状的热疲劳龟裂以及淬火零件在磨削过程中的裂纹均属于这种形式。
剥离裂纹产生在表层很窄的区域内,其轴向和切向作用着压应力,径向为拉应力状态,裂纹平行于零件表面,表面淬火和渗碳零件冷却后发生硬化层的剥落均属于此类裂纹。它的产生与硬化层内组织不均匀有关,例如合金渗碳钢以一定速度冷却后,其渗碳层内的组织为:外层极细珠光体+碳化物,次层为马氏体+残余奥氏体,内层为细珠光体或极细珠光体组织。由于次层马氏体的形成比体积最大,体积膨胀的结果使表层的轴向、切向作用着压应力,径向为拉应力,并向内部发生应力突变,过渡为压应力状态,剥离裂纹产生在应力急剧过渡的极薄区域内。一般情况下,裂纹潜伏在平行于表面的内部,严重时造成表面剥落。若加快或减馒渗碳件的冷速,使渗碳层内获得均匀一致的马氏体组织或极细珠光体组织,可防止这类裂纹的产生。此外,髙频或火焰表面淬火时,常因表面过热,沿硬化层的组织不均匀性也容易形成这类表面裂纹。
显微裂纹与前述四种裂纹不同,它是由显微应力造成的。高碳工具钢或渗碳工件淬火过热再经磨削后出现的沿晶裂纹,以及淬火零件不及时回火引起的裂纹都与钢中存在显微裂纹并随之扩张有关。
显微裂纹须在显微镜下检查,其通常在原奥氏体晶界处或马氏体片的交界处产生,有的裂纹穿过马氏体片。研究表明,显微裂纹多见于片状孪晶马氏体中,原因是片状马氏体在髙速长大时相互撞击产生很高的应力,而孪晶马氏体本身性脆,不能产生塑性变形使应力松弛,因而易产生显微裂纹。奥氏体晶粒粗大,产生显微裂纹的敏感性增大,钢中存在显微裂纹会显著降低淬火零件的强度和塑性,从而导致零件早期破坏(断裂)。
避免高碳钢零件的显微裂纹,可采取较低的淬火加热温度、获得细小马氏体组织,并降低马氏体中含碳量等措施。此外,淬火后及时回火是减少内应力的有效方法。试验证明,经200℃以上充分回火,在显傲裂纹处析出的碳化物有“焊合”裂纹作用,这可显著降低显微裂纹的危害。
以上为依照裂纹分布形态讨论裂纹成因和防止办法。实际生产中因钢材质量、零件形状以及冷热加工工艺等因索影响,使裂纹的分布不尽相同。有时热处理前已存在裂纹,在淬火过程中裂纹进一步扩大;有时也可能同一零件几种形式的裂纹同时出现。对此种种情况则应根据裂纹的形态特征、断口的宏观分析、金相检査,在必要时配合化学分析等方法,从材料质量、组织结构到产生热处理应力的原因来综合分析,寻找产生裂纹的主要原因,然后确定有效的防止措施。
裂纹的断口分析是分析产生裂纹原因的重要方法。任何断口都有一个发生裂纹的起点。淬火裂纹通常以放射状裂痕的收敛点为裂纹的起点。若裂纹的起点存在于枣件表面,说明裂纹是在表面承受过大拉应力造成的。倘若表面不存在夹杂物等组织缺陷,而有严重刀痕、氧化皮、钢件的尖角或结构突变部位等应力集中因素,均可促使裂纹的产生。如若裂纹的起点在零件内部,则与材料的缺陷或内部残余拉应力过大有关。正常淬火的 断口呈灰色细瓷状,如果断口呈深灰色粗糙的状态,则是过热或原始组织粗大造成的。一般地讲,淬火裂纹的玻断面上应无氧化颜色,裂纹四周也没有脱碳现象。假如裂纹四周有脱碳现象或裂纹的断面上有氧化顔色,则表明零件在未淬火前已存在裂纹,在热处理应力影响下使原裂纹扩大。如若在零件裂纹附近看到偏析分布的碳化物、夹杂物,说明裂纹与原材料的碳化物严重偏析或存在夹杂物有关。若裂纹仅出现在零件的尖角或形状突变部位而又没有上述现象,说明裂纹是因零件结构设计不合理或防止裂纹的措施不当,由过大的热处理应力造成的。
另外,化学热处理和表面淬火零件的裂纹大多呈现在硬化层附近,改善硬化层组织、降低热处理应力是避免表面裂纹的重要途径。