安锻产品
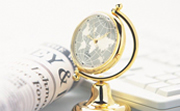
铝合金控制臂精密锻造工艺与锻造设备选择
前言
铝合金以其密度小、比强度高、加工性好等优点在各个领域都得到了广泛的应用,为了达到节能减重的效果,美国、日本和西欧等发达国家都在不断加大对铝合金锻造材料及其工艺的研发力度,铝合金锻造技术更是被作为一项核心技术来重点支持和发展。
自1956年起,世界铝产量就一直居有色金属首位。目前世界铝加工材产量为3000万吨/年,其中板、带、箔材占57%,挤压材占38%。由于铝合金锻造材成本高,生产技术难度大,仅在特别重要的受力部位采用,因此在加工材中所占比例较小,为2.5%。随着汽车工业的不断发展,对汽车轻量化的要求越来越高。据报道,轿车质量每减少10%,燃油消耗可降低6%~8%,因此,以铝合金为代表的轻质材料在汽车零部件中的应用日趋广泛。据估计,全球铝锻件每年的需求量高达100万吨,而目前全世界的年产量仅约为80万吨,尚不能满足市场需求。在汽车行业,目前铝合金轮毂的使用量达到数十亿个,且每年仍在以20%的速度增长。
铝合金三角臂是汽车转向系统的关键部件,其形状复杂,成形难度大。本文将从工艺与装备角度详细介绍一条铝合金控制臂精密锻造自动化生产线。
铝合金的锻造工艺特点
⑴塑性较低。铝合金塑性受合金成分和锻造温度的影响较大,而且塑性对变形速度的敏感程度随合金元素的含量不同而不同,当合金元素含量增加时,铝合金塑性不断下降,且对变形速度的敏感程度也增强。大多数铝合金都为正应变速率敏感材料,即流动应力随着变形速率的降低而减小,因此,对于航空用大型铝合金锻件,往往采用油压机或者水压机成形,对于中小型锻件则可采用螺旋压力机或者机械压力机制造。
⑵粘附性强。由于铝和铁可以固溶,因此,铝合金在锻造过程中经常发生粘模现象。一般认为,锭子油可以起到较好的润滑效果,近年来,美国Acheson等公司也开发出了适合工业应用的铝合金润滑剂。国内也有公司自己配制油基或水基润滑剂,使用效果也很好。
⑶锻造温度范围窄。大多数铝合金的锻造温度范围都在150℃以内,有些甚至只有70℃,因此,在锻造生产中,往往需要采用多次加热的方法来确保铝合金具有良好的可锻性。尤其是对产品性能要求严格的航天和军工产品,在最终成形时往往采用等温锻造的方法进行生产。
⑷工序变形量小。铝合金锻造一般不允许少工序、大变形,以免导致粗晶或者产生裂纹,因此,往往需要将总变形量进行合理分配,制坯工序对于最终产品的成形结果影响较大。由于工件经过若干工序后,温度往往低于所要求的锻造温度,故需要再次加热。
铝合金控制臂锻造工艺的设计
最近,北京机电研究所开发出一种汽车用铝合金控制臂锻造工艺,并以此为基础建立起一条铝合金控制臂自动锻造生产线,目前已经移交客户使用。
该产品的锻造工艺流程为:中频加热→辊锻→弯曲、压扁→二次加热→预锻、终锻→切边、冲孔、校正。铝合金控制臂的锻造过程如图1所示。
(a)辊锻
(b)弯曲
(c)压扁
(d)预锻
(e)终锻
(f)切边、冲孔、校正
图1 铝合金控制臂的锻造过程
生产线主要工序的设备选型
根据产品特点和生产节拍,选定400kW中频感应加热炉作为首次加热设备,如图2所示。该设备感应加热速度快,加热温度可控,毛坯温差小,且易于实现自动化。此外,在出料口设有温度分选装置,对过温和欠温坯料进行识别和分选。
图2400kW中频感应加热炉
辊锻:φ560mm自动辊锻机
根据产品规格和变形特点,参考辊锻机型号和技术参数,最终选用φ560mm自动辊锻机(其技术参数见表1),如图3所示。该设备配有喂料机械手和辊锻机械手,其中,辊锻机械手为机械联动式,其通过特定的机械杆系结构,将轧辊的回转运动直接转换为机械手沿辊锻方向的往复运动,结构简单,动作可靠,与辊锻机配合实现全自动操作。辊锻一个工作循环(4道次辊锻)为12~14s,生产节拍快,辊锻件尺寸稳定、精度高。此外,将坯料大头端作为辊锻机夹钳的夹持端,在后续工艺中,可将其作为锻件的一部分,避免了多余的夹持工艺料头,提高了材料利用率。
图3 φ560mm自动辊锻机
表1 φ560mm自动辊锻机技术参数
辊锻模外径/mm |
560 |
辊锻可使用宽度/mm |
700 |
辊锻件最大长度/mm |
870 |
辊锻中心可调整量/mm |
20 |
轧辊转速/r·min-1 |
52 |
最大坯料尺寸/mm |
φ100 |
手臂纵向行程/mm |
758 |
手臂横向行程/mm |
550 |
纵向位置调整量/mm |
400 |
单道次横向行程/mm |
87~170 |
可夹持最大重量/kg |
30 |
主电机功率/kW |
55 |
弯曲、压扁:3150kN机械压力机
根据工艺需要,选取一台3150kN机械压力机(其技术参数见表2)用于弯曲和压扁,如图4所示。该设备采用闭式钢板整体焊接结构,机身垂直刚度好、角变形小,结构合理,能够承受强烈震动。压力机滑块采用八面矩形导轨,在工作过程中能保持较高的精度。
图43150kN机械压力机
表23150kN机械压力机技术参数
型号 |
YS1-315 |
最大公称压力/kN |
3150 |
最大公称力行程/mm |
8 |
最大滑块行程/mm |
320 |
行程次数/次·min-1 |
25~40 |
最大装模高度/mm |
600 |
装模高度调节量/mm |
120 |
立柱间距离/mm |
1440 |
工作台尺寸(长×宽)/mm |
1400×900 |
工作台孔直径尺寸/mm |
250 |
工作台板厚度/mm |
200 |
侧面开口(宽×高)/mm |
750×660 |
滑块底面尺寸(左右×前后)/mm |
1300×750 |
电机功率/kW |
37 |
外形尺寸(长×宽×高)/mm |
2900×2000×4700 |
二次加热:连续式加热炉
根据自动化生产的特点,并考虑便于维护的需要,最终采用连续式加热炉。该炉采用链带式结构,生产节拍为20s/件。铝合金锻造对于温度的要求十分严格,对炉温控制的要求也很高,炉温均匀性要求达到±4℃,温度控制精度达±2℃。如图5所示为二次加热炉内的工件。
图5 二次加热炉内的工件
预锻、终锻:25000kN离合器式螺旋压力机
根据数值模拟和计算结果,该产品的锻造变形力为20000kN左右,25000kN离合器式螺旋压力机(亦称高能螺旋压力机,如图6所示)的相关技术参数(表3)能够满足该种零件的锻造需求。此外,离合器式螺旋压力机的滑块在全部行程上均能发挥出额定的能量和打击力,有助于提高成形效率。打击次数、打击能量、打击力均可进行预选,并能在触摸屏上实时显示工作中的相关参数。该设备对于打击终了位置的控制更为可靠,除了电气控制以外,还设计有惯性盘控制机构,超行程打击后会自动脱开。这种压力机具有多工位锻造的能力,可以满足工艺设计中将预锻和终锻模膛布置在一副模具中成形的要求。
图6 25000kN离合器式螺旋压力机
表3 25000kN离合器式螺旋压力机技术参数
名义吨位/kN |
25000 |
最大吨位/kN |
31500 |
滑块速度/mm·s-1 |
500 |
滑块最大行程/mm |
625 |
最大输出能量/kJ |
750 |
最小装模高度/mm |
960 |
工作台垫板尺寸(长×宽)/mm×mm |
1400×1400 |
主电机功率/kW |
132 |
装机总功率/kW |
172 |
设备地面以上高度/mm |
约7900 |
切边、冲孔和校正复合工序:3150kN机械压力机
3150kN机械压力机的结构及参数在前面的弯曲与压扁工序中已有详细的描述,此处不再赘述。
固溶处理:连续式固溶处理炉
固溶处理根据自动化生产的要求采用连续式固溶处理炉,如图7所示为固溶炉内的产品。
图7 固溶炉内的产品
生产线的平面布局
主要设备的选型完成后,根据厂房原有条件,综合考虑物流需求,最终确定的整条生产线的平面布置如图8所示。
图8 生产线平面布置图
1—中频加热炉 2—辊锻机 3—3150kN机械压力机 4—二次加热炉
5—25000kN离合器式螺旋压力机 6—3150kN机械压力机 7—固溶炉
由图8可知,该生产线由中频加热炉、辊锻机、3150kN机械压力机、二次加热炉、25000kN离合器式螺旋压力机以及固溶炉组成。各工序之间通过机器人进行工件传送,实现自动化生产,如图9所示。
图9 生产线(局部)
为了提高效率,该生产线配备5台机器人,用于不同工序之间工件的传送。R1机器人负责从辊锻机出料到弯曲之间的工件搬运以及弯曲到压扁工位的搬运;R2机器人则负责将工件从压扁工位放入二次加热炉;R3机器人将二次加热后的工件从出炉口放入预锻工位;R4机器人承担将预锻工件搬运到终锻工位,并将终锻后的工件放到中转料台的工作;R5机器人将工件从中转料台放到切边、冲孔工位,并将最终产品放入固溶炉中。最终批量生产出的产品如图10所示。
图10 批量生产出的产品
由于该生产线采用多关节机器人而不是桁架类机械手进行工件传送,因此具备较好的柔性,既可满足单一品种大批量的自动化生产要求,在更换模具和部分机器人夹钳以及部分辅助工具后,也可进行不同品种、不同批量的其他产品生产。这对于现代企业所强调的柔性化和订单化生产十分有利。
结语
目前我国铝合金锻造行业还处于起步阶段,在基础研究、技术装备、产品种类和质量、生产规模和管理水平等方面都和国外先进水平存在较大差距。本文介绍的汽车用铝合金控制臂锻造技术和装备,具有投入少、成本低、柔性好、生产效率高等优点,年生产能力可达60万件。该生产线的建成投产,对于打破国外垄断、促进我国铝合金锻造行业的工艺进步和效率提升,具有很好的示范作用。